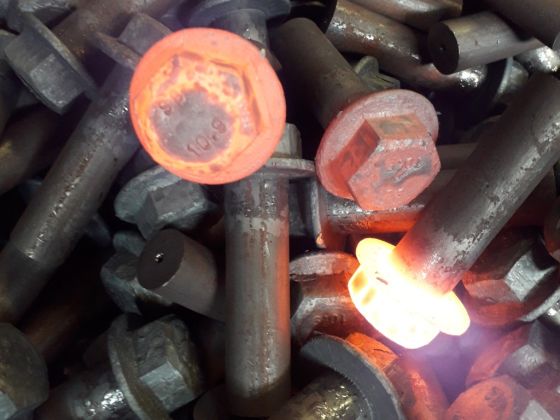
Adapt, innovate, develop: Manchester’s Smith Bullough has a bolt making history that can be traced back over a century. By marrying tradition with modern manufacturing practices while expanding its expertise, the firm has found itself well placed to deal with the current highly unusual situation. Director Tim Garton speaks with Torque Magazine…
Perhaps like many UK businesses in general, Smith Bullough came into 2020 with a fair degree of positivity.
Smith Bullough Director Tim Garton picks up the story: “The market had been quite sluggish during the second half of 2019 with the uncertainty generated by the Brexit saga.”
With the protracted period of deadlock largely being resolved following the December General Election, the electorate gave the new government the authority and remit to “get Brexit done”, taking much of the unpredictability of the situation away.
Garton continues: “Returning after the 2019 Christmas break, we were enthusiastic about the opportunities that 2020 would present, but coronavirus appeared and wrecked the budgets of every company in the world!”
Happily for this fastener business, Smith Bullough was well placed going into the Covid‐related disruption: “Although our plans have been shocked, they have not been wrecked. Smith Bullough is in the fortunate position that its business is in the supply of non‐standards and specials in a variety of head shapes, grades and finishes but often in fairly modest quantities, and that satisfies the needs of a diverse range of industrial users. Our appeal is often an ability to supply locally‐made goods in a quick time period.”
Nevertheless, the pandemic did mean immediate measures were required to operate in the lockdown, Garton explains: “Fundamental charges needed to be implemented to comply with the social distancing and bio security measures required to combat the virus. The measures that we now take for granted under lockdown, we had to develop and put into operation.
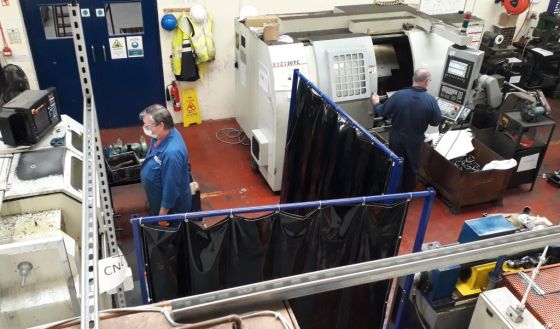
“There wasn’t a guide or manual that could be referenced apart from www.gov.co.uk and that was changing daily as the scientists gained knowledge as how best to combat the pandemic.
“Close involvement with all employees was necessary as shielding, self‐isolating and suspected Covid‐19 symptoms manifested into a very scary workplace situation. Notwithstanding all these issues we stayed open and continued to forge and manufacture quality nuts and bolts which is a great achievement from all our employees.”
Garton also believes some of the changes – like home working and video meetings – have been a benefit and will endure to some degree long after the virus is beaten.
BEYOND COVID
Smith Bullough is a high‐class jobbing factory with a wide range of capabilities and an extensive range of products on offer, principles that its Director says put it in good stead.
“It is a great strength for us and a benefit for our customers as it will, hopefully, allow us to tough out the economic depression that is bound to follow the ending of the generous Furlough scheme.”
Smith Bullough deals with fasteners in carbon, alloy, stainless and exotic materials, with the business largely built on carbon and alloy material fasteners that can then be heat treated to the required grade and then followed by a surface coating or plating, as needed.
In recent years, the firm has developed further into stainless steel, duplex, super duplex and exotic material production following staff training and the recruitment of people with the relevant and required skills. In terms of trends, Garton says Smith Bullough has experienced a greater demand for special sizes of stainless and exotic fasteners, because, he says: “The marketplace understands that we are in a good position to supply their non‐standards and specials in these materials.”
KEEPING LEAN AND THE CARBON FOOTPRINT
This fastener business is not just developing in terms of materials expertise either. The last time that Torque spoke with Smith Bullough, we heard how the firm had focused on Lean Awareness workshops and this remains an area that the business is centring on.
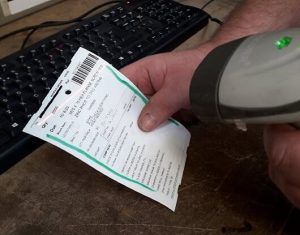
“Despite the challenges of the coronavirus restrictions, lean manufacturing and the elimination of waste remain as most important tasks for the business. We have developed a network of KPIs, some with data downloaded in real time directly from our integrated computer software system. These measures are constantly evolving and provide important statistics to assist decision making.
“An important tool that we have developed in‐house and take extreme pride with is the digitalisation of our production process. Product route cards contain a unique bar code and each process is scanned at the start and finish of the operation by the operator, using strategically placed computer data logging terminals. The data captured provides accurate and immediate information on the job that permits quick progress data to be given to customers. Important information collected at this stage feeds KPIs that monitor on time delivery, production efficiencies and other important measures.
“Employees in all sectors of our business want to improve performance and deliver improved customer satisfaction and the KPIs assist in achieving this goal.”
That lean philosophy and reduction of waste play into that other hot topic of sustainability. Smith Bullough believes the fastener biz has some way to go to fully embrace the movement.
"Sustainability and the measurement and reduction of the business generated carbon footprint is of great importance to all. At present there is not much importance placed on it from within the fastener industry sector in UK. If the industry doesn’t begin to get to grips with these issues then the Government will impose measures. Perhaps the CBM & BIAFD can orchestrate manufacturers and distributors and help to lead a sustainability programme for the industry.”
EXPANDING EXPERTISE
Two years ago, Smith Bullough acquired Werneth, which brought about enhancements in the firm’s expertise, says Garton: “Our capability in drilling, especially cross drilling through heads and threads, has improved considerably and we now generate very accurate and precise drilled and chamfered holes. The 2018 influx of ex‐Werneth machines promoted this improvement but it was not an easy development as the drill machines and jigs in most instances needed major maintenance or replacement.”
Naturally, any further business acquisition interest was brought to an abrupt halt with the advent of the coronavirus pandemic, but – if the project is capable of adding value and concerning non‐standard or special fasteners – then Smith Bullough has an open mind, Torque can reveal.
This year Smith Bullough continues to develop its business, in both the ferrous and non‐ferrous areas, following the purchase of a couple of bar‐fed machines. Garton fills in the details: “The most impressive of the bar‐fed machines is a fully automatic 12 station CNC turning centre with live tooling. It offers a 300mm diameter powered chuck along with a 550mm turned length capacity that can deliver a 10 micron accuracy. We will look forward to showing off this machine, even if social distancing means that it has to be by video link or YouTube!”
Thoughts nevertheless turn back to coronavirus, which has been another great challenge for all industry, says Garton: “Those businesses within the fastener industry who were making bolts in the 1970s, when GKN gave up making bolts, and are still producing now have good reason to be proud.”
He concludes: “Smith Bullough has been in business for more than 100 years and has a proven capability to adapt, innovate and develop. The business has good plans and strategies to further improve the business regardless of the twists and turns that may present themselves in our fastener journey.”
This article was first published in Torque Magazine. Don't get a copy? Subscribe here and find our back issues in our archive.