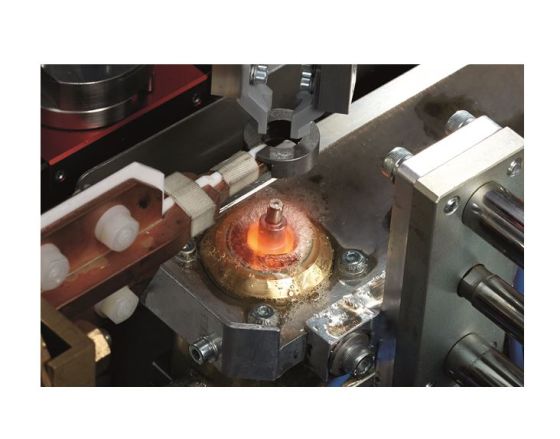
The HEICO Group now offers modern induction hardening technology especially for small-sectioned mass products. With the help of its own mechanical engineering section and the consultation of various specialists in the field of hardening technology, machines with high process control as well as a high unit performance have been developed.
The inductive hardening process involves the appropriate, partial hardening of cold forged parts. With the help of this precise hardening process, customers’ special component requirements – especially regarding surface hardness – can be optimally fulfilled. Customers appreciate this process, as it is possible to selectively harden highly stressed parts of components. Therefore, individual customer requirements for extraordinary geometries of components are fully practicable. HEICO Group’s induction hardening systems apply in the medium and high frequency range. In addition, a tempering furnace is used, which helps to relax the parts and prevent cracking. 100% control with eddy current testing also serves as an important tool for high quality control. A further advantage is the resulting metallography and structural analysis, which are begin in the technologically advanced, in-house testing laboratory by trained specialist personnel. HEICO Group has a fully automatic hardness tester at its disposal, which operates in the test load range of 0.05-30kg. In addition, the customers of HEICO have the option of receiving graphical test profiles and / or individual test reports, ensuring that the quality of the hardening process meets their own requirements.
The entire inductive hardening process is fully controlled using modern process monitoring software. The induction hardening systems and the tempering furnace comply with the CQI-9 standard, which is necessary for the automotive industry in evaluating heat treatment processes. Furthermore, an adapted statistical process control is executed throughout the process, another tool to provide HEICO Group customers optimum quality of their hardened parts.
HEICO’s management is proud to have taken this important step towards the entire vertical integration of the company. The investment in its own inductive hardening plants ensures sustainable
flexibility regarding customer requirements, a shorter total delivery time and an increase of HEICO’s own technical expertise.
The future development, improvement and adaptation of the entire plant to modern technical standards are priorities for HEICO. The company's own toolmaking department provides the important key foundations. Tools and inductors can be produced independently and in-house by qualified employees to match the requirements of customer orders. For this, the customer can rely on the knowledge and skills of more than 100 years of cold forging experience.
Together with the entire direction of the company aimed at the high quality standards of the automotive industry, a synergy effect is created from which all customers of HEICO Group benefit sustainably and noticeably.