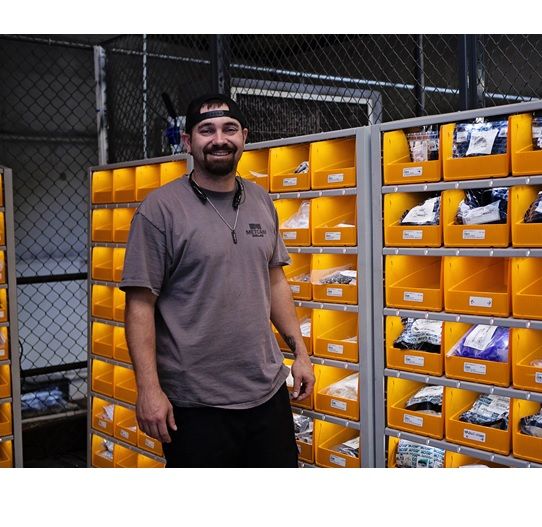
Apex Supply Chain Solutions – a specialist in intelligent, automated dispensing – has launched Actylus, a new smart Kanban/Vendor Managed Inventory system to manage stock and replace the need for manual counting, flags, labels and cards.
Crucially, the technology is ideal for items such as fasteners and rivets and after establishing itself in the US market, Apex Supply Chain Solutions is looking to grow its presence in Britain.
Actylus: How does it work?
Actylus manages stock with a smart bin technology designed to solve stock replenishment issues, sending automated alerts and re-order notifications to suppliers to eliminate the need for counting trips, safety stock and emergency orders. It aims to keep lines up-and-running, boost supply chain productivity and grow bottom-line revenues.
Powered by Trajectory Cloud, a secure business intelligence platform that connects existing systems, Apex says that the Actylus smart bin system improves productivity, visibility, reliability and accessibility throughout a business operation. The Trajectory Cloud is able to monitor the Actylus system to see when items need restocking, simultaneously tracking usage patterns and trends through a reporting system.
CASE STUDY: ACTYLUS IN THE US FASTENER INDUSTRY
Is your system futuristic but your bins stuck in the past? Many bin arrangements offer no visibility into the flow of materials at any given moment, which leads to a cascading series of impacts that hurt the bottom line.
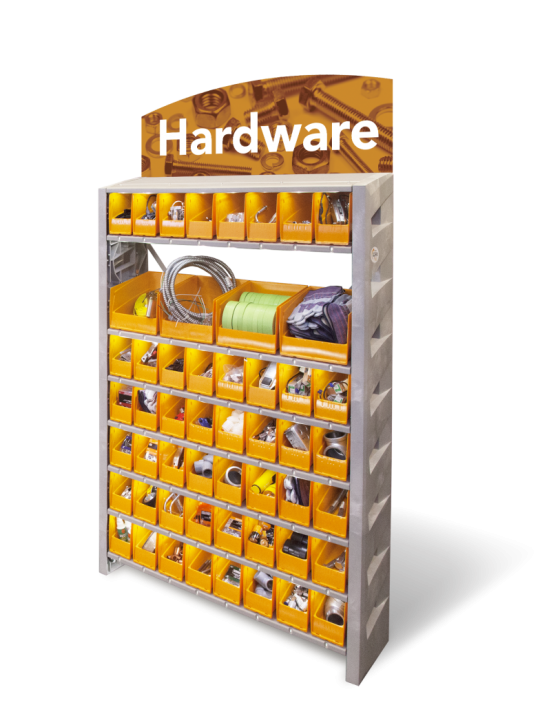
Employees who know that the bin system doesn’t work well end up taking more than what they need so they can work without interruption, potentially resulting in chronic stock-outs for other employees. Management deals with stock-outs with costly emergency orders, or sending employees on “milk runs” for supplies.
This is a haphazard method of working, Apex Supply Chain Technologies says: “Bins represent an old, manual process, while the rest of the world is moving to real-time supply chain visibility and just-in-time delivery.”
Assembly Fasteners (AFI), a US-based global distributor of products and services to large industrial customers, specialises in vendor managed inventory (VMI) programs, within which it manages its customers’ inventory levels.
For AFI and its customers, the old method of restocking bins was time-consuming. Seeking a new way of doing things, it began looking at automated
bin systems and Apex Actylus Smart Bins stood out. AFI president Hugh Watson explains: “We could tell from the get-go that this would be a
game-changer for us.”
AFI deployed Actylus Smart Bins with two contract manufacturing customers that each has facilities of more than 9,000m2. Actylus automatically sends current inventory levels for each bin to the Apex Trajectory Cloud platform, which then alerts AFI and its customers when levels drop to pre-set minimums. With real-time visibility every bin always has enough. Multiple configurations in the number of rows and size of the bins are available, so Actylus can be customised for any setting.
“We don’t lose time scanning bins anymore,” Watson explains. “Now we get alerts by email, place our orders for replacement parts and make one trip to replenish the bins.”
Technicians who used to spend time on manual counts immediately regained a full day each week because Actylus checks each bin for them, saving around two months of time over a year, Apex calculates.
“We work in a competitive industry, so the Apex Actylus system gives us a different look and appeal. It helps us to separate ourselves from competitors that are often right next to us on the shop floor.”